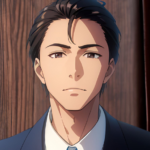
ゴム業界で働く中で気付いた事を
日々コラムとして執筆していきます。
今回はVol39 自動車業界におけるゴム塗装外観部品の色合わせと品質管理:OEM、IATF16949、PPAPによる保証
というコラムを書いていきます。
自動車業界では、ゴム塗装外観部品(ドアシール、トランクガスケット、エンジン部品など)の色合わせや外観品質が車両全体の印象を左右します。ゴム部品はその機能性だけでなく、外観にも高い品質基準が求められるため、色合わせや塗装の均一性、耐久性の管理が非常に重要です。この外観品質は、**OEM(Original Equipment Manufacturer)の基準や、IATF16949といった国際的な品質マネジメントシステム、さらにPPAP(Production Part Approval Process)**によって保証されます。これらの規格に基づいて、部品の外観は厳格に評価され、品質が確保される仕組みが整っています。
(出典)https://rike-syu.com/blog/about-introducing-the-structure-and-parts-of-automobiles-and-the-industry/
1. ゴム塗装外観部品の色合わせ
ゴム部品に塗装を施す理由は、外観の美しさを追求するだけでなく、耐久性や紫外線耐性、化学的な耐性を向上させるためでもあります。特に色合わせは、車両のデザインや外装の一貫性を保つために不可欠です。色合わせや外観品質は、OEM基準やIATF16949、PPAPを通じて厳格に管理され、部品が一定の品質を維持することが求められます。
1.1. 色合わせの重要性
- 外観の統一性: 車両のデザインにおいて、ゴム部品の色合わせが他の部品(メタル、プラスチック、内装など)と調和しているかが重要です。特に、外部に露出するゴム部品(ドアシール、バンパーの周囲、ウィンドウガスケットなど)は、車両全体の印象に大きな影響を与えます。
- 消費者の印象: 色が一致しないと、品質に対する印象が悪化し、消費者からの信頼性に影響を与えることがあります。
- ブランドの一貫性: 各自動車メーカーは、ブランドカラーやデザインに一貫性を持たせるため、ゴム部品の色合いを厳格に管理します。
1.2. 色合わせの方法
色合わせは通常、以下の方法で行われます。
- 色見本作成: 製造前に、塗装するゴム部品の色見本を作成し、全体の色調やテクスチャーが車両の外装に合致しているかを確認します。
- 色測定機器の使用: 自動車業界では、色差計や分光光度計などの精密機器を使用して、ゴム部品と車両外装の色差を測定し、基準値と一致するか確認します。これにより、厳密な色合わせが可能になります。
- 試作・確認工程: 色見本やサンプル部品を使って試作を行い、実際に車両に取り付けた際の外観を確認します。必要に応じて、調整を行い、最終的な色合いが決定されます。
2. ゴム塗装外観部品の品質管理
ゴム塗装外観部品の品質管理は、部品の外観、機能、耐久性を確保するために不可欠です。自動車業界では、塗装後の外観チェックや機能チェックが厳密に行われ、製品が高い品質基準を満たすことを保証します。
2.1. 品質管理の主な項目
- 色一致: 色の一致が最も重要な品質管理項目の一つです。色差が車両全体のデザインに影響を与えるため、色差を±1-2程度に収めることが目標です。
- 塗膜の厚さ: 塗装の厚さが均一であることが重要です。塗膜が薄すぎると、耐久性や耐候性が低く、逆に厚すぎると見た目が不自然になり、柔軟性に問題が生じることがあります。
- 塗装の均一性: ゴム表面に塗装が均等に施されているか、むらがないかをチェックします。塗装のムラや剥がれは、部品の品質を損ねる要因となります。
- 耐久性テスト: ゴム部品に塗装した後、その耐久性を確認するために、紫外線、酸性雨、塩水などに対する耐性をテストします。これにより、塗装が長期間安定して車両の外観を維持できるかを確認します。
- 傷や欠けの検査: 塗装後のゴム部品に傷や欠けがないかを確認します。これらの問題は、部品の機能に直接影響を与える可能性があるため、厳密な検査が行われます。
2.2. 品質管理のプロセス
品質管理は、通常、以下のステップで行われます。
- 入荷検査: 塗装に使用するゴム部品の素材や基材が規格に合致しているかを確認します。これにより、最初の段階で不良品を排除します。
- 塗装前検査: 塗装を施す前に、ゴム部品の表面に欠陥や汚れがないかをチェックし、必要に応じて表面処理(研磨や洗浄)を行います。
- 塗装後検査: 塗装後、色差や塗膜の厚さ、均一性を測定し、基準をクリアしているか確認します。
- 最終検査: 完成したゴム塗装外観部品は、車両に取り付ける前に最終的な外観チェックを行います。これには、色合いや傷の有無、塗膜の密着度などの確認が含まれます。
3. PPAP(生産部品承認プロセス)による外観品質の保証
**PPAP(Production Part Approval Process)**は、自動車業界で製造される部品の品質を確保するための標準化されたプロセスであり、特に外観品質が重要なゴム塗装外観部品において、製品が設計通りであることを確認するために使用されます。
3.1. PPAPの目的
PPAPの目的は、新しい部品や変更された部品が所定の品質基準を満たしていることを確認することです。ゴム塗装外観部品においても、色合いや塗装の仕上がりが基準に合致しているかを評価するため、PPAPが重要な役割を果たします。
3.2. 外観に関連するPPAPの要素
PPAPでは、部品の外観品質を確認するために、以下の要素が評価されます:
- 色合いの一致: 部品の色が設計通りであるか、他の部品との一致を確認します。色差計や分光光度計を使用して、厳密な色合わせが行われます。
- 塗装の均一性: 塗膜の厚さや均一性が確保されているかを確認します。PPAPでは、製造中に発生する可能性のある色ムラや塗装の不均一を排除するため、細かな検査が行われます。
- 耐久性の検証: 塗装後のゴム部品の耐久性を、紫外線や酸性雨に対するテストを通じて確認します。これにより、部品が長期間安定して外観を保てるかを評価します。
(出典)https://www.keyence.co.jp/ss/imagemeasure/sokushiri/news/006/
3.3. PPAPの承認と品質保証
PPAPの承認プロセスでは、外観に関する品質基準が満たされていない場合、部品の修正や再試作が求められます。このプロセスを経て、最終的に部品が生産に適した品質であると確認されると、量産が開始されます。
4. まとめ
自動車業界におけるゴム塗装外観部品の色合わせと品質管理は、車両の外観や消費者の信頼性を維持するために非常に重要です。**PPAP(生産部品承認プロセス)**は、外観品質に関する厳格な基準を満たすための重要なプロセスであり、色差や塗膜の均一性、耐久性などが確認されます。これにより、部品が常に高品質であり、車両全体のデザインが一貫性を持つことが保証されます。厳密な品質管理とPPAPによる外観品質の保証により、最終的に消費者に対して満足のいく製品が提供されるのです。
コメント