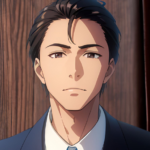
ゴム業界で働く中で気付いた事を
日々コラムとして執筆していきます。
今回はVol.38ゴム製品の品質向上を目指す!離型剤の塗布方法と不良原因、対策まとめ
というコラムを書いていきます。
ゴム製品の製造において、離型剤は非常に重要な役割を果たします。正しい塗布方法が守られなければ、製品に欠けや損傷、さらには金型汚れが発生し、最終的な品質に大きな影響を与えます。この記事では、離型剤の塗布方法、よくある不良原因、そしてその対策について詳しく解説します。
離型剤の塗布方法
離型剤はゴム製品が金型からスムーズに取り出せるようにするために使用されます。適切な塗布方法を守ることで、製品品質の向上と生産効率の改善が実現できます。
1. スプレー容器の選定と管理
離型剤を塗布するためには、適切なスプレー容器の選択とその管理が重要です。以下の点をチェックしましょう:
- 圧力スプレー容器:一定の圧力で均等に離型剤を塗布することができます。
- エアレススプレー:より細かく均等な霧状で塗布できるため、高精度が求められる場合に有効です。
- 定期的な点検:スプレーノズルが詰まっていないか、容器内の残量を確認し、スプレーガンの状態を常にチェックすることが重要です。
(出典)https://www.anest-iwata.co.jp/products-and-support/coating-equipment/mold-release-agent/tof1-h
(出典)https://www.monotaro.com/note/readingseries/tosouqa/0209/
2. スプレー方法
スプレー方法は、製品品質に直結します。以下のポイントを守りましょう:
- スプレーの距離:スプレー容器と金型の距離は約20~30cmが適切です。近すぎると過剰に塗布され、遠すぎると膜が薄くなります。
- スプレー角度と速度:スプレーガンは金型に対して垂直に近い角度で均等に動かし、一定の速度で動かします。これにより均一に離型剤が塗布されます。
- スプレー量の管理:過剰に塗布せず、薄く何度もスプレーすることで、均等な膜厚を実現します。
3. 乾燥時間と環境管理
離型剤は塗布後に十分に乾燥させることが必要です。乾燥不良を防ぐため、温度や湿度が管理された環境で乾燥を行うようにしましょう。乾燥時間は使用する離型剤により異なりますので、製造元の推奨に従うことが大切です。
離型剤による不良原因
離型剤の塗布方法が不適切だと、様々な不良が発生します。以下は、よくある不良原因です。
1. 型汚れ
- 原因:過剰な離型剤の塗布や不均一な塗布により、型表面に離型剤が残り、汚れとして蓄積します。
- 影響:金型が摩耗し、製品にムラや欠けが生じ、取り出し時に問題が発生します。
2. 製品の欠けや損傷
- 原因:離型剤が不均等に塗布されている場合、金型との摩擦が大きくなり、ゴム製品が金型に引っかかり、欠けや損傷が発生します。また、乾燥不良や成形不良も原因となります。
- 影響:製品の強度や外観に影響を与え、最終的に顧客満足度の低下や信頼性の損失に繋がります。
3. 取り出し困難
- 原因:離型剤が薄すぎたり、乾燥不十分で金型に残ると、ゴムが型に付着し、取り出しが困難になります。
- 影響:製品が金型に引っかかることで、破損や傷が発生し、生産効率が低下します。
離型剤の不良対策
不良を防ぐためには、以下の対策を徹底することが重要です。
1. 適切な離型剤の使用
- 過剰塗布を避ける:適量を使用し、均等に塗布します。過剰塗布を避けることで型汚れを防ぎます。
- 均等な塗布:スプレーガンの距離や角度、動きに注意し、離型剤を均一に塗布します。
2. 金型の定期的なメンテナンス
- 金型の清掃:金型表面に残った離型剤や汚れを定期的に除去します。金型の状態が良好でないと、製品に不良が発生します。
- 型合わせの確認:金型が適切に合わせられているか、摩耗や損傷がないかを確認します。
3. 適切な乾燥時間と環境
- 乾燥の確認:離型剤が完全に乾燥したことを確認してから成形を開始します。乾燥時間が足りないと、型に残留物が残り、不良を引き起こします。
- 乾燥環境の管理:温度や湿度が適切な環境で乾燥を行うことで、離型剤の膜厚を均等に保つことができます。
まとめ
離型剤の塗布方法はゴム製品の品質を守る上で非常に重要です。適切なスプレー容器の選定や塗布方法、乾燥時間を管理することで、型汚れや製品の欠け・損傷を防ぐことができます。定期的な金型のメンテナンスや乾燥環境の管理を行い、不良のリスクを減らすことで、生産性を向上させ、顧客満足度を高めることができます。品質向上を目指して、これらのポイントをしっかりと押さえ、安定した製造プロセスを実現しましょう。
中国語版
提升橡胶产品质量!模具脱模剂涂布方法、不良原因及对策总结
在橡胶产品的生产过程中,模具脱模剂起着至关重要的作用。只有采用正确的涂布方法,才能有效避免产品缺损、损伤以及模具污染等问题,确保最终产品的质量。本文将详细介绍模具脱模剂的涂布方法、常见的不良原因以及相应的对策。
模具脱模剂的涂布方法
模具脱模剂的作用是使橡胶产品能够顺利从模具中取出,避免橡胶与模具之间的摩擦。采用适当的涂布方法可以有效提高产品质量,并改善生产效率。
1. 选择和管理适当的喷雾容器
涂布模具脱模剂时,选择合适的喷雾容器并对其进行管理非常重要。以下几点需要特别注意:
- 压力喷雾容器:压力喷雾容器能够提供稳定的压力,从而均匀地涂布脱模剂。
- 无气喷雾器:无气喷雾器可以喷出更细腻、更均匀的雾状,适用于精度要求较高的生产环境。
- 定期检查:定期检查喷雾器的喷嘴是否堵塞,并确保容器内脱模剂的剩余量充足。
2. 喷雾方法
喷雾方法直接影响到脱模剂的涂布质量。遵循以下原则,可以确保涂布均匀,避免出现不良:
- 喷雾距离:喷雾容器与模具表面之间的距离应保持在20~30厘米之间。如果距离过近,脱模剂可能涂布过量;如果距离过远,涂层会过薄。
- 喷雾角度与速度:喷雾器应尽量与模具表面垂直,并保持一定的喷射速度,确保脱模剂均匀涂布。
- 喷雾量的控制:避免涂布过量,推荐采用多次薄涂的方式,这样能够确保膜厚均匀。
3. 干燥时间与环境管理
涂布脱模剂后,必须确保其充分干燥。干燥不充分会导致脱模剂残留在模具表面,影响后续的生产过程。干燥时间根据所使用的脱模剂类型有所不同,最好按照厂商的建议进行调整。同时,确保干燥环境的温度和湿度适宜,以保证脱模剂均匀干燥。
模具脱模剂不良原因
不正确的涂布方法会导致各种不良情况的发生,影响产品质量。以下是常见的不良原因:
1. 模具污染
- 原因:过量使用脱模剂或涂布不均匀,导致脱模剂残留在模具表面,逐渐积累形成污染。
- 影响:模具表面磨损,产品出现涂层不均、缺损或划痕,取出产品时出现困难。
2. 产品缺损与损伤
- 原因:涂布不均匀导致摩擦过大,橡胶与模具粘连,取出时导致产品缺损或表面划伤。
- 影响:影响产品外观和强度,导致客户不满和信任度下降。
3. 取出困难
- 原因:脱模剂涂布不足,或者脱模剂干燥不完全,导致橡胶产品与模具黏附。
- 影响:取出产品时,产品容易损坏或受损,生产效率降低。
模具脱模剂不良的对策
为了避免上述不良问题的发生,采取以下措施至关重要:
1. 正确使用脱模剂
- 避免过量使用:脱模剂涂布应适量,避免过多或过少,确保涂层均匀。
- 均匀涂布:在涂布时,保持喷雾器的距离、角度和移动速度一致,确保涂布均匀。
2. 定期维护模具
- 定期清洁模具:模具表面应定期清洁,去除脱模剂和污垢。模具维护良好,能够避免污染和减少不良的发生。
- 检查模具对接:确保模具正确对接,避免因模具不合适而导致的产品缺损。
3. 适当的干燥时间和环境
- 确保干燥:涂布脱模剂后,确保其充分干燥后再进行成型,以防干燥不足导致的脱模剂残留。
- 控制干燥环境:管理好干燥环境的温度和湿度,确保脱模剂的膜厚均匀。
结论
模具脱模剂的涂布方法对橡胶产品的质量至关重要。通过选择合适的喷雾容器、正确的喷雾方法、合理的干燥时间和环境管理,可以有效避免型污、产品缺损和损伤等问题,从而提高生产效率和产品质量。通过定期清洁和维护模具,以及控制涂布量和涂布均匀性,可以确保生产过程顺利,最终确保客户满意度和品牌声誉。
コメント